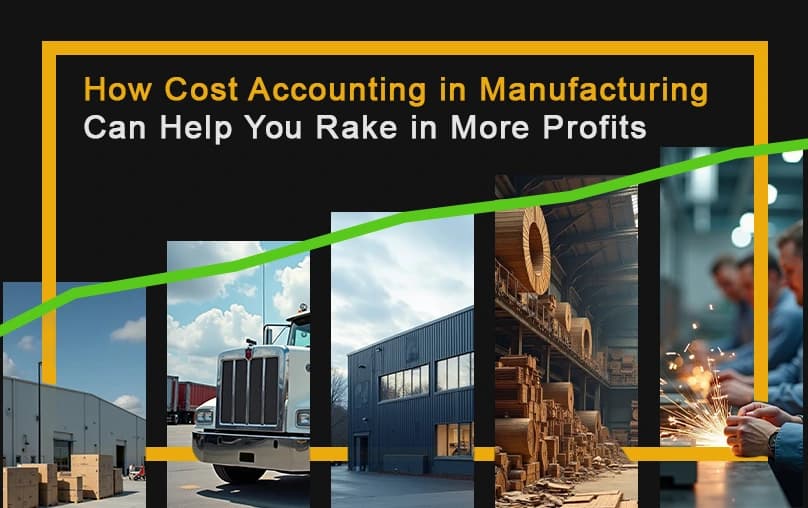
Ever wondered how successful manufacturing companies stay ahead of the game and keep their profits soaring? The secret sauce isn’t just cutting costs randomly, it’s about knowing where and how to trim the fat without sacrificing quality or efficiency.
That’s where cost accounting in manufacturing steps in. Whether you’re launching a new manufacturing business or scaling your operations, understanding your manufacturing costs is non-negotiable if you want to stay competitive and profitable.
In this blog, we are diving into:
• What manufacturing costs are
• The key components of manufacturing costs
• Why tracking and analyzing these costs can help you make smarter, and more profitable decisions
What Are Manufacturing Costs?
Manufacturing costs (aka product costs) are all the expenses a company incurs while making a product. These costs fall into two major buckets:
1. Direct costs
2. Indirect costs
Accurately calculating these costs helps manufacturers spot inefficiencies, set the right product prices, and ultimately, boost profits. And according to McKinsey’s research cutting down manufacturing costs while improving productivity is the key to staying competitive in the modern manufacturing landscape.
Breaking Down Direct Manufacturing Costs
Direct manufacturing costs are expenses that can be attributed directly to the production of a specific product. They include costs related to:
1. Direct Materials:
For instance, if you operate a furniture manufacturing business, your direct materials might include:
• Wood for furniture frames, legs, and panels
• Upholstery fabric for sofas and chairs
• Foam and cushioning for seating comfort
• Paints and finishes for aesthetics and durability
But there’s more to it than just the purchase price of these materials. You also need to factor in:
• The procurement costs (finding suppliers, negotiating contracts)
• The transportation costs of shipping the raw materials
• Import duties and taxes on materials sourced internationally
• Storage and warehousing expenses before they’re used in production
2. Direct Labor
This includes wages and benefits paid to employees directly involved in building the product. Examples include:
• Carpenters crafting and assembling wooden components
• Upholsterers sewing and attaching fabric to furniture frames
• Painters applying protective coatings and final finishes to enhance durability and aesthetics.
Beyond basic wages, direct labor also covers:
• Overtime Pay
• Payroll Taxes
• Employee Benefits (health insurance, retirement plans, workers’ comp)
When you add up all your direct costs, you get the Cost of Goods Sold (COGS), a key figure in determining profitability.
Indirect Manufacturing Costs
Indirect manufacturing costs (aka factory overhead) cover everything else that supports production but isn’t tied to a specific product. These include:
• Factory rent or mortgage payments
• Utilities (electricity, gas, water)
• Machine maintenance & depreciation
• Insurance & property taxes
• Factory supervisor salaries
According to a study conducted by McKinsey, these overhead costs can account for 8-12% of total manufacturing costs. Keeping track of them is crucial for determining product pricing and setting the right profitability margins.
The Profit-Boosting Benefits of Cost Accounting in Manufacturing
Now that we’ve covered the nuts and bolts of manufacturing costs, let’s talk about how cost accounting can help you boost profits and make better business decisions.
1. It Helps You Control Costs Like a Pro:
By tracking manufacturing costs, you can spot unnecessary expenses and optimize spending.
For example, let’s say your raw material costs are skyrocketing. Cost accounting can help you:
• Identify which raw material costs are increasing, allowing you to explore alternative suppliers
• Identify wasteful spending in procurement
• Provide insights into inventory costs, helping you make informed decisions on stock management
Working with a strategic accounting partner can help you dig deep into historical cost data, identify trends, and pinpoint where money is leaking. With these insights, you could potentially cut manufacturing costs by 10% or more!
2. It Helps You Set the Right Prices to Stay Competitive
If you don’t know exactly how much it costs to manufacture your products, you can’t price them correctly.
Cost accounting ensures that you:
• Know your true production costs
• Add the right markup for profitability
• And stay competitive without underpricing your products
Example: A furniture manufacturer realized that rising wood prices were cutting into margins. By analyzing cost data, they switched to a more cost-effective wood supplier while maintaining quality, reducing material costs by 15% without impacting product pricing.
This proves that manufacturers who track and control costs can strategically lower prices without hurting profitability, giving them a major competitive advantage.
3. It Helps You Assess Product Profitability
Not all products are created equal, some bring in massive profits, while others might be dragging you down.
Cost accounting helps you:
• See which products are worth producing
• Identify hidden costs eating into profits
• Decide whether to scale up or discontinue certain product lines
According to the study titled The Impact of Cost Control on Manufacturing Industries’ Profitability, controlling costs related to labor, materials, and overhead can significantly boost profitability. Simply put, knowing your numbers = making smarter business moves.
Cost Accounting = More Profits, Smarter Decisions
If you’re running a manufacturing business, cost accounting isn’t just a nice-to-have, it’s a must.
At the end of the day, cost accounting helps you to put more money in your pocket while keeping your business agile, competitive, and well-positioned for long-term success in the manufacturing industry.
So, are you keeping track of your manufacturing costs? If not, it’s time to start, because your bottom line depends on it.
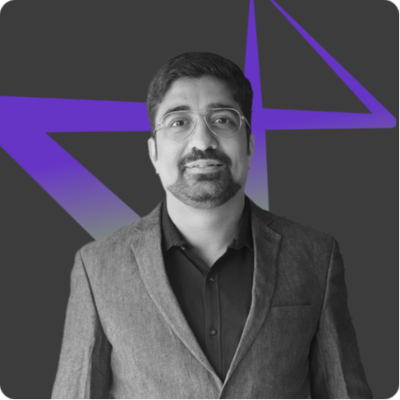
Shekhar Mehrotra
Founder and Chief Executive Officer
Shekhar Mehrotra, a Chartered Accountant with over 12 years of experience, has been a leader in finance, tax, and accounting. He has advised clients across sectors like infrastructure, IT, and pharmaceuticals, providing expertise in management, direct and indirect taxes, audits, and compliance. As a 360-degree virtual CFO, Shekhar has streamlined accounting processes and managed cash flow to ensure businesses remain tax and regulatory compliant.
You might also like:
- Rental Property Depreciation Secrets Every Landlord Should Know
- Accounting for Gift Cards: A Simple Guide for Restaurant Owners
- Cash Without Compromise: How a Sale-Leaseback Transaction Can Supercharge Your Business
- The Role of Outsourced Accounting in Profit-Driven Property Management
- Why Ignoring Veterinary Accounting Could Hurt Your Practice?
Listen Exclusive Podcast On